Pin Clamp Design Eliminates Downtime
A large automotive manufacturer had an application utilising vendor-supplied products prone to premature failure due to contamination (weld slag). The problem was so severe, the manufacturer assigned personnel to maintain the products. Every three days, maintenance cleaned the products to keep production running, resulting in additional overhead expenses, lost manpower, and production downtime.
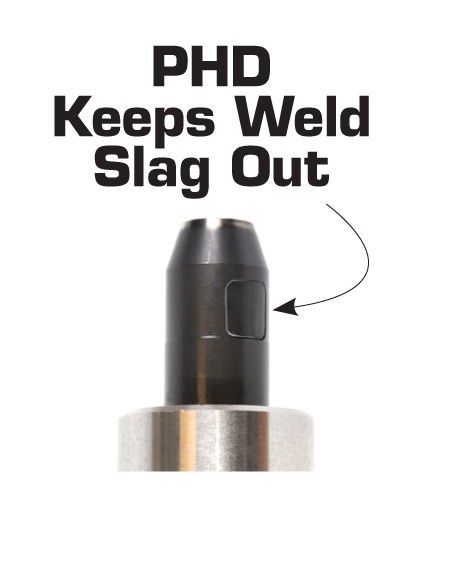
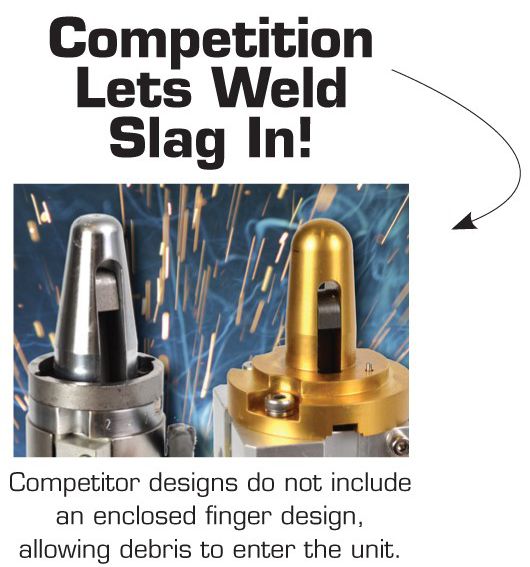
PHD’s Clamp division worked with the manufacturer and determined the Series PLK Clamp was an ideal fit for the application’s requirement. Unlike that of competitive models, PLK Clamps have a completely enclosed finger and pin design that minimizes the ingression of contamination. In addition to the virtually contamination-free design, PLK Clamps come standard with an internal lock that holds the part in place during pressure loss or as emergeny stop. This means that the part will not fall, thereby reducing the threat of bodily injury.
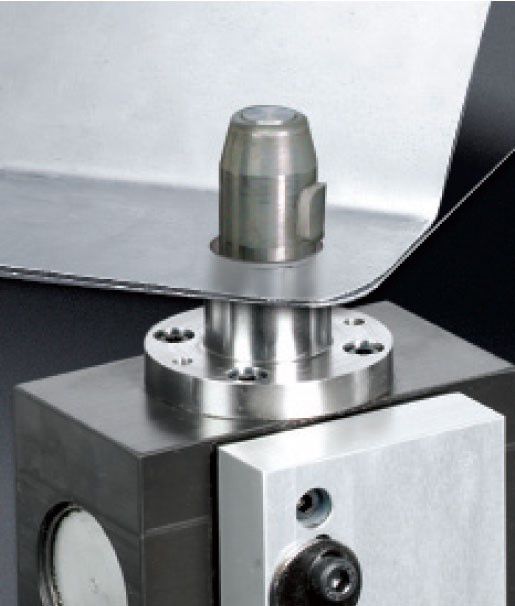
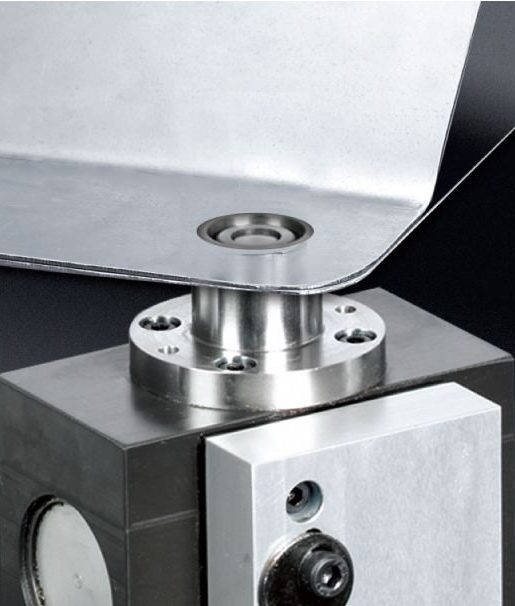
After installing the PLK Clamps, the manufacturer was able to reduce overhead expenses, reallocate their maintenance crew, and eliminate production downtime. PLK Clamps have been and continue to be used throughout the world in similar applications, all with great success. Click here to view the internal workings of the PLK Clamp.
For more information about PHD, click here…
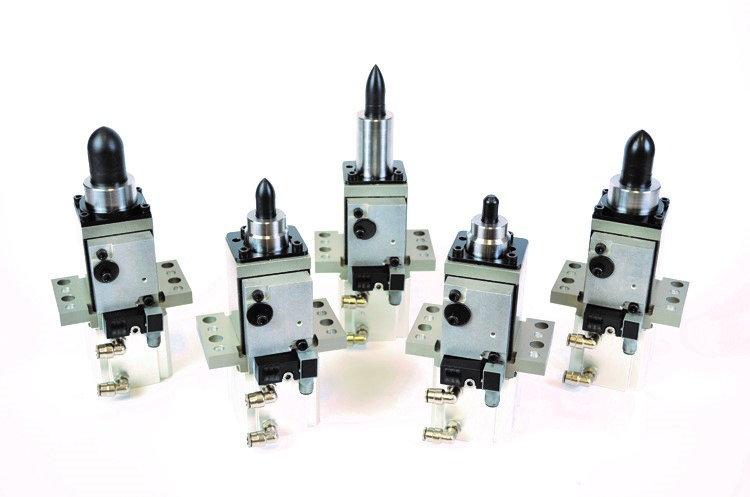